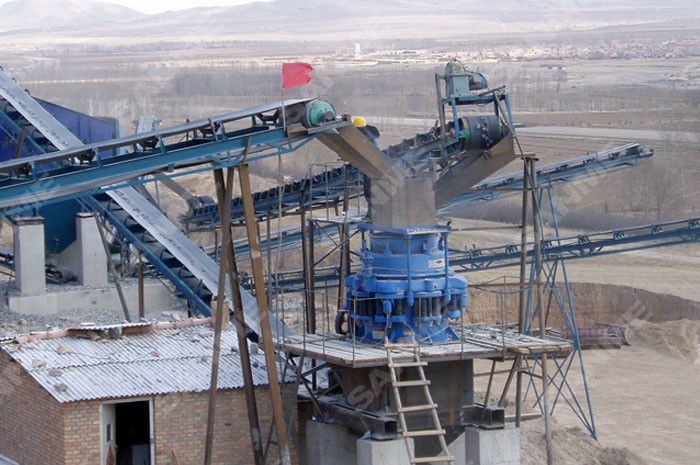
400Kw Metallurgy Feeding 460mm Cone Crusher Machine
2025-7-17
The dry sand production line is a process system that can remove mud powder from sand without water washing and produce machine-made sand that meets construction standards. Its core lies in replacing traditional wet sand washing with dry screening and powder selection technology, getting rid of water resource dependence, and achieving environmental protection and efficient production. The following is a detailed introduction:
1、Core equipment and process flow
Equipment composition
Crushing equipment: jaw crusher (coarse crushing), impact crusher (medium and fine crushing, such as “stone hitting stone” or “stone hitting iron” series).
Screening equipment: circular vibrating screen (multi-layer screen classification), coarse and fine powder separator (powder selection machine, separating 0-0.075mm stone powder).
Conveying equipment: belt conveyor (connecting various processes), elevator (vertical material transportation).
Environmental protection equipment: pulse bag dust collector (control dust emission), negative pressure dust removal system (fully enclosed production environment).
Auxiliary equipment: hopper (raw material storage), silo group (finished product storage).
Process flow
Raw material crushing: 0-40mm aggregate is crushed by jaw crusher and then sent to impact crusher by belt conveyor for further crushing.
Screening and grading: The crushed material enters the circular vibrating screen, and the materials larger than 5mm are screened out and returned to the impact crusher for re-crushing. The materials smaller than 3mm are partly produced as finished products and partly returned for re-crushing, and the materials smaller than 3mm enter the powder selector.
Stone powder separation: The powder selector separates 0-0.075mm stone powder, and 0.075-3mm and 3-5mm materials form the finished product pile.
Environmental treatment: The dust removal system collects dust in the production process to avoid dust pollution.
2、Technical advantages
Zero water consumption
No need for sand washing, completely get rid of water source restrictions, especially suitable for arid areas or water shortage scenarios.
Normal production can still be carried out in low temperature environment in winter, avoiding the shutdown problem of wet production line due to icing.
Outstanding environmental performance
The fully enclosed production environment is equipped with a pulse bag dust collector, and the dust emission concentration is ≤30mg/m³ and the noise is ≤90dB, meeting environmental protection requirements.
Stone powder can be recycled (such as roadbed cushion layer, cement unburned brick raw materials) to achieve zero resource emissions.
Low production cost
Saves water resource input, sewage treatment equipment and operating costs in the water washing process.
High degree of automation, only 2 operators per shift, labor costs reduced by more than 50%.
Controllable quality of finished products
Through the variable frequency speed control system, the fineness modulus (2.3-3.0 adjustable) and stone powder content (3%-15% adjustable) of the machine-made sand can be quickly adjusted.
The finished sand grade is reasonable, the particle shape is round, and it meets the Class I construction sand standard, and the concrete strength is increased by 10%-15%.
Strong adaptability
It can handle medium and high hardness materials such as river pebbles, pebbles, limestone, granite, and even industrial waste such as slag.
The plane occupies only 35m×20m, with a compact layout, suitable for projects with limited space.
3、Application scenarios
Infrastructure construction: concrete aggregate production for highways, railways, bridges, ports and other projects.
Urban construction: commercial concrete mixing stations, municipal engineering sand and gravel supply.
Environmental protection field: construction waste recycling sand making, tailings comprehensive utilization.
Arid areas: sand and gravel production in water-scarce areas such as Northwest and North China.
4、Development trend
With the tightening of environmental protection policies and the increase in demand for sand and gravel aggregates, dry sand production lines are developing in the direction of intelligence, modularization and large-scale. For example, the V9 series environmentally friendly sand making building system of Henan Huayi Engineering adopts a fully enclosed conveying and negative pressure dust removal design to achieve unmanned production. The single-line production capacity can reach 500 tons/hour, and the floor area is reduced by 30%, becoming an industry benchmark.