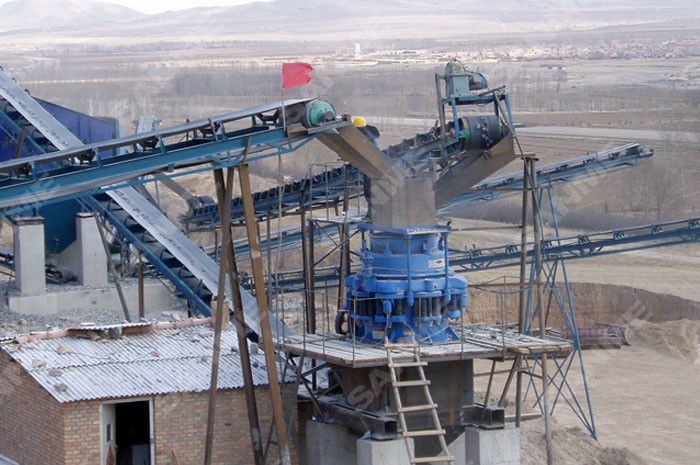
400Kw Metallurgy Feeding 460mm Cone Crusher Machine
2024-4-29
There are significant differences between jaw crushers and impact crushers in multiple aspects.
Firstly, from the perspective of working principle, the jaw crusher uses a curved extrusion method to crush materials. When the electric motor drives the belt and pulley, and the moving jaw moves up and down through the eccentric shaft, the material is sandwiched between the two jaw plates, and is crushed through the friction and impact of the jaw plates. The impact crusher uses impact energy to crush materials. The electric motor drives the rotor to rotate at high speed. When the material enters the plate hammer action area, it collides and breaks with the plate hammer on the rotor, and is then thrown towards the counterattack device to break again. This process is repeated until the material is broken to the required particle size.
Secondly, in terms of applicable materials, jaw crushers are more suitable for crushing medium hardness and brittle materials, such as limestone, quartz, sandstone, etc. The impact crusher is more suitable for handling soft materials such as limestone and coal gangue, as well as medium hard materials such as river pebbles and dolomite.
In addition, the shape of the crushing chamber between the two is also different. The crushing chamber of the jaw crusher is V-shaped, while the crushing chamber of the impact crusher is C-shaped. This makes the flow of materials in the crushing chamber of the impact crusher better when processing materials, making it less prone to blockage, thereby improving production efficiency.
Finally, from the perspective of crushing effect, the jaw crusher crushes stones through the squeezing of two jaws, with a crushing particle size range generally between 50mm and 1500mm. The specific crushing particle size will vary depending on different models of jaw crushers and factors such as the hardness and humidity of the crushed materials. The jaw crusher can crush various high hardness ores, such as granite, basalt, as well as ordinary hardness limestone, calcite, etc. The finished products it crushes often contain needle shaped and flat stones, with larger discharge particle sizes.
The impact crusher uses the plate hammer on the high-speed rotating rotor to impact and crush materials, with a crushing particle size of no more than 500mm and a compressive strength of no more than 350MPa. The material crushed by the impact crusher has a relatively smooth particle shape and uniform particle size, making it suitable for crushing concrete, limestone, coal, and other hard materials. It has high efficiency, good crushing effect, strong safety and reliability, and can also save energy.
In summary, there are significant differences between jaw crushers and impact crushers in terms of working principle, applicable materials, crushing chamber shape, energy consumption, discharge particle size, and crushing effect. When choosing which crusher to use, it is necessary to comprehensively consider the specific material characteristics and crushing requirements.
So, should we choose jaw crushing or counterattack crushing in the primary crushing stage of ore?
The choice between jaw fracture and counterattack fracture mainly depends on the nature of the material, crushing requirements, and the configuration of the production line.
Jaw crusher, also known as jaw crusher, is a type of coarse stone crushing jaw crusher series. It has the characteristics of high crushing ratio, uniform product particle size, simple structure, reliable operation, easy maintenance, and economic operating costs. The main component is the jaw plate, which is driven by an electric motor to drive the belt and pulley, causing the moving jaw to move up and down. The material is crushed by multiple forces such as compression, rubbing, and grinding between the jaw plates. Therefore, jaw fracture is more suitable for coarse crushing operations of various soft and medium hard ores.
Counterattack crusher, also known as counterattack crusher, is a processing equipment that uses impact energy to crush materials. The working principle is that the electric motor drives the rotor to rotate at high speed, and the material enters the plate hammer action area and collides with the plate hammer on the rotor to break, and then is thrown towards the counterattack device to break again. This process is repeated until the material is broken to the required particle size. Counterattack crushing has the characteristics of good particle size and high crushing efficiency, and is suitable for medium to fine crushing operations of materials with compressive strength not exceeding 350MPa and relatively soft hardness.
Overall, both jaw fracture and counterattack fracture have their own characteristics and applicability. When selecting, consideration should be given to material characteristics, crushing requirements, and the overall configuration of the production line. For materials with high hardness that require coarse crushing, jaw breaking may be more suitable; For materials with moderate hardness and the need to obtain good particle shape, counterattack may be more suitable. In practical applications, it is also possible to use a combination of jaw crusher and counterattack crusher according to the front and rear configuration of the production line, in order to achieve better crushing effect.